Drum Up, Ready, Go!
Cutting to length made easy: electrical wholesaler Löffelhardt opts for the new large drum system from Kabelmat.
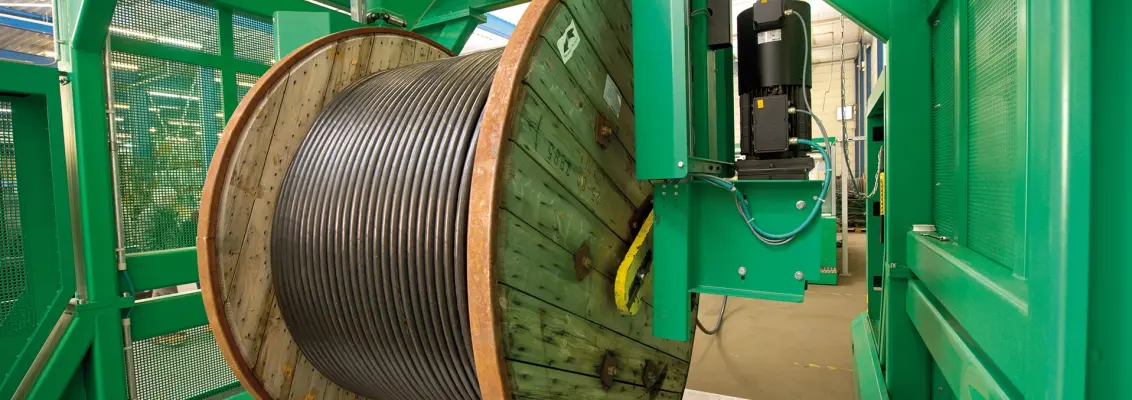
The empty cable drums are stacked up to the ceiling in the warehouse of electrical wholesaler Löffelhardt. On the floor, large, wound cable drums stand in rank and file. Order picker Sascha Brinkmann lifts one of the large drums with the forklift. He neatly drives around a shelf and heads for the big green machine. In front of the machine's unwinder, he sets down the wooden drum, which weighs several tonnes with its black ground cable that is almost as thick as an arm. The colossal reel sways gently until it finds its rest position. Andreas Schebesta, management board member and Head of Logistics and IT at Löffelhardt, points to the machine and says: “That is our large drum system from Kabelmat. With it, we can cut cable drums that weigh over six tonnes and have a size of two and a half metres in length for our customers with no problem.”
At the touch of a button, Brinkmann moves the portable unwinder, the so-called PORTROL, over the drum. The unwinding unit glides over rails embedded in the ground and stops over the load, which weighs several tonnes. Here, the intake comes to the drum rather than vice versa – differentiating this large drum system from many others.
Sascha Brinkmann can therefore generally cut the huge cable drums to length on his own. During busy times, they work in pairs – one collects and brings the drums and the other operates the machine. This is even quicker, as the PORTROL can be loaded and unloaded from both sides. The forklift therefore never travels empty and the machine is constantly working. On the left and right, the tapered spindles move into the holes in the wooden drum, fix it and subsequently move it during unrolling while telescoping arms lift the drum. Brinkmann threads the end of the cable into the length gauge on the equipment table opposite before moving it on and fixing it to the empty drum. Safety laser scanners monitor different areas depending on the work stage, so the machine stops immediately if a member of staff walks into a danger zone. Electrical wholesaler Löffelhardt has partnered with Kabelmat since 1996. At that time, family company Löffelhardt was automating its high rack storage and designed a special machine alongside Kabelmat to cut cable directly beside the conveyor system. To open up new market sectors, Löffelhardt then extended its cable area in 2000 with a large drum system and again relied on the winding technology professionals. “The system has been running for 15 years and is still in such good condition that we decided to keep it as a reserve rather than sell it, Andreas Schebesta says.
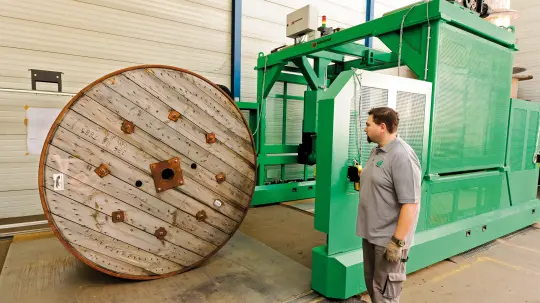
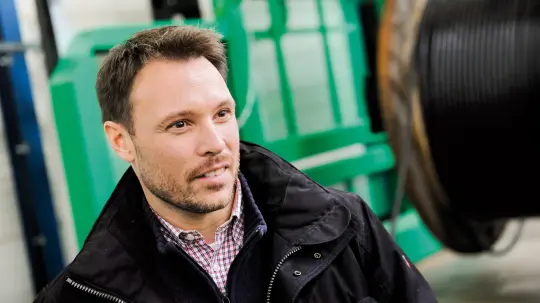
VAST STOCK ASSORTMENT
In 2013, Löffelhardt decided to invest in a new system. This would allow processing of even larger and heavier drums. As a result, the company can buy in and supply greater lengths and volumes. Finally, in stock for its customers, Löffelhardt also has thick underground cables as well as sensitive BUS and control cables, installation cables and rubber tubes, remote communication, flexible electronic and data cables. The new system will not only take on the additional business but also completely replace the existing concept – i.e. also cutting the smaller drums to length quickly and reliably. It should also raise the productivity of the process to such an extent that Löffelhardt will have additional capacity for future company growth. “This would then result in configuration of the movable PORTROL, single-person operation and electronically synchronised winder and unwinder drives,” Andreas Schebesta says. The latter plays a major role in two respects – performance and productivity of the system.
SYNCHRONIZED DRIVE
Electronics control the winders and unwinders such that the cable always has exactly the same rate even at a high speed. With the synchronised drives, the system can wind quicker without too much tension on the cable, which would damage it. Moreover, despite the high speed, a uniform installation pattern is achieved. “In addition to delivery speed, we therefore also fulfil the second big promise to our customers: quality.
“The uniform installation pattern gives them the assurance that the cable can be unwound and installed properly without damage,” Schebesta recounts. Brinkmann has wound the exact cable length from one drum to another. The system places the large drum back on the ground and the PORTROL returns to the waiting position. If it were a typical spring day, Brinkmann’s colleague Ralph Müller, the order picking manager, would have already provided the next drum on the unwinding side and the machine would need only to collect it. However, today is a quiet February day, so he climbs back into the forklift himself to finish this order and cut the product to length for the next customer.
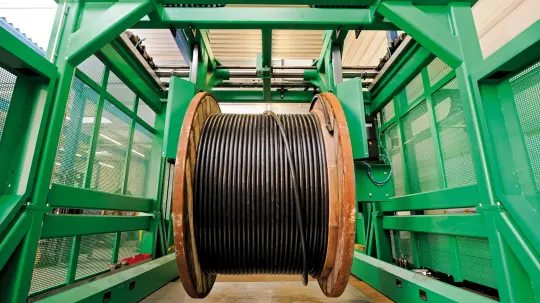
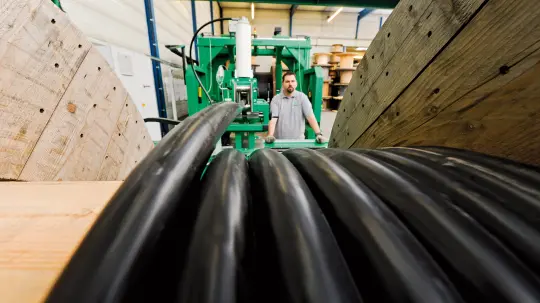