Cable Lengths at the Touch of a Button
Purchasing goods online is recording rapid growth not only in the consumer sector but also in the industrial space. Distributors such as TIM in particular are benefiting from this. To be able to meet the increased demands in the area of cables and wires with a 24-hour delivery guarantee, a cable cutting system from Kabelmat is used.
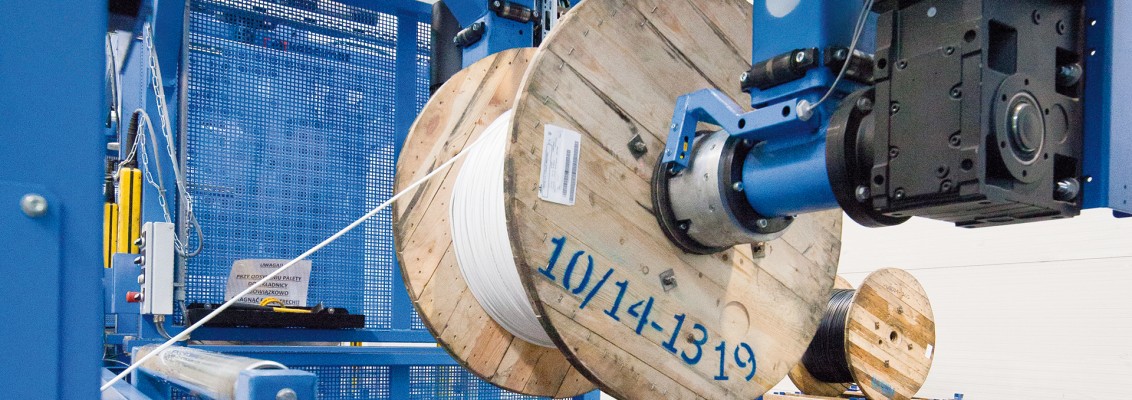
Since 1987, TIM SA (Technology, Innovation, Mobility) from the Polish town of Siechnice has served the Polish market with products and services for measuring and control technology as well as the electrical and electronic fields.
MANUAL PROCESSES KEPT TO A MINIMUM
In their facility, there are 1800 spaces available for cable drums in high-level storage, which are served by automatic storage operating units. Taking the cable drums by pallet, these fully automated storage units supply three partially automated cable cutting stations currently in use. The new AUTOLOG coiling plant with automatic drum loading allows the processing of drums with a diameter up to 1600 mm (60 in). Since 2007, TIM has obtained cable cutting systems from Kabelmat Wickeltechnik GmbH in Glatten, a subsidiary of the HELUKABEL group. The market leader for coiling systems in the cable and wire industry supplies almost all devices and machines for storing, coiling and cutting cables, wires, steel cables, pipes, hoses and extruded profiles. The AUTOLOG system supplied for TIM has a “drum to machine” design. “We offer a very high level of automation, which cannot be compared to many systems, particularly with those from small suppliers,” says Kabelmat Wickeltechnik GmbH Sales Manager Manfred Wößner proudly.
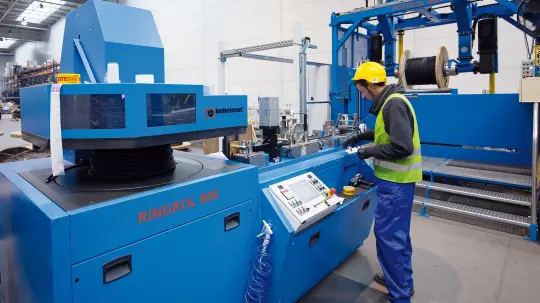

TECHNOLOGY MADE IN GERMANY
The digital drive technology of the cable cutter consists of electric servomotors with controlled frequency inverters. Here, the drum is powered from the middle rather than from the flange, which is often the case. This provides better concentricity. “High speeds with optimum traction control are the second most important feature alongside safety,” Wößner says. “We drive at speeds of up to 250 m (820 ft) per minute.” Another advantage is traction control with built-in cable store. A special function of this storage technology governs the traction when winding sensitive cables. The store functions as a buffer by synchronising the unwinder and the winder in order to keep the traction forces low. Additionally, movement technology allows the store to be moved away for direct coiling, which is necessary for thicker or stiffer cables. “Our machines have a length measuring system calibrated in accordance with PTB (German federal physical technical institute) standards, which is recognised all over Europe,” explains Wößner. All the relevant data, such as production length or residual cut length are transmitted by data exchange between the machine and the warehouse logistics system. “The data transfer from the drum conveyor sections of other manufacturers to the machines is also important. We have created all the necessary interfaces for data exchange,” Wößner says. “We really appreciate the option of being able to couple all data systems together so our EDP communicates with the warehouse systems of our customers,” Maciej Posadzy, COO of TIM SA, emphasises. “Even better, these interfaces are all very easy to control.”
A LOT OF CUTS PER DAY
“The more efficiently the machines work, the better and more quickly we are able and the fewer staff we need to look after our customers, who naturally look at price,” says Posadzy, explaining the rationale. “The cuts must not become too expensive, with up to 800 cuts made per day. The productivity of the new systems is now six to seven times better than the old systems,” adds Posadzy.
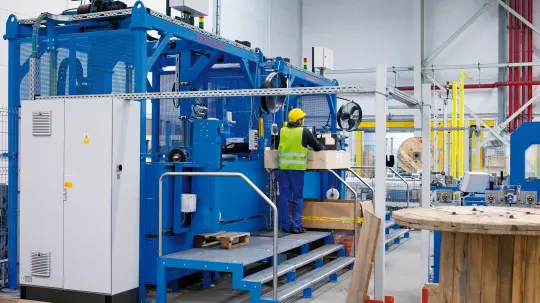