Put to the Ultimate Test – Part 2: Bending Tests
During the development of our cables and wires, we vigorously test each product in our testing laboratories. In the second part of our series, we’ll introduce you to bending tests.
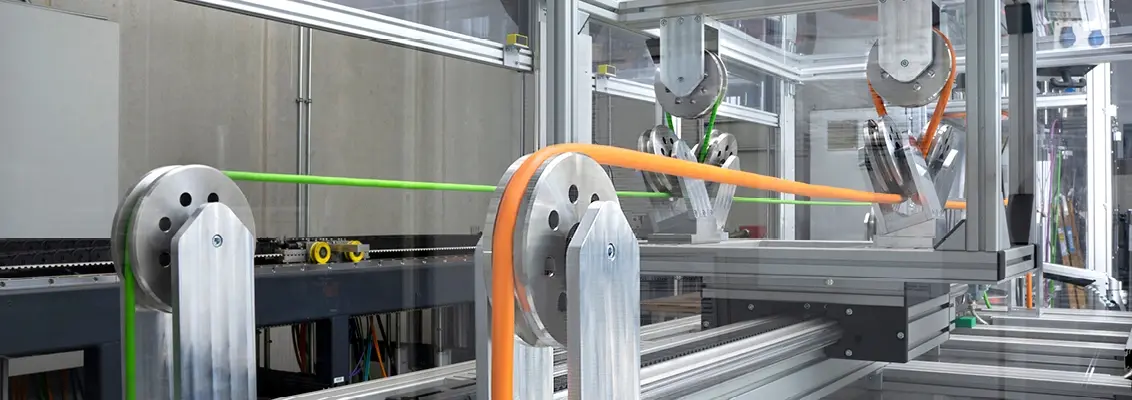
In dynamic applications typical to mechanical and plant engineering or drive and automation technology, cables and wires are frequently subject to mechanical bending stresses. Although these stresses also occur in static installations, they are much higher in dynamic applications because the force and direction of movement are constantly changing. Such situations are pure stress for the cable. The wires, core insulation and sheathing material are squeezed on the inside and stretched on the outside, and the cable can tear. Degradation, up to and including cable damage, leads to faults and functional failures.
To make sure our cables and wires reliably withstand day-to-day stresses, we perform bending tests on them in our testing laboratories. These tests are normally laid down in the specifications from customers or in standards such as those from the VDE. Our testing equipment simulates bending stresses with diverse loads and bending radii in order to verify the mechanical strength of the cable. Our test methods include alternate bending tests using two rollers (as per DIN EN 50396 6.2) and three rollers (as per DIN EN 50396 6.3). Parameters such as speed, acceleration and traverse path can be easily varied to create realistic test conditions for a diversity of use cases.
Every cable we develop must comply with the strict test criteria. The copper wires, insulation material and sheathing material must show no signs of degradation after testing. Moreover, the entire stranding as well as braiding and twisting must maintain their original form. Only in this way can it be guaranteed that the cable will function reliably in day-to-day use, even after millions of bending cycles.
Even more, we have purpose-designed drag chain tests for cables used in energy chains. You can read about these in the next part of our series.
Ask the expert
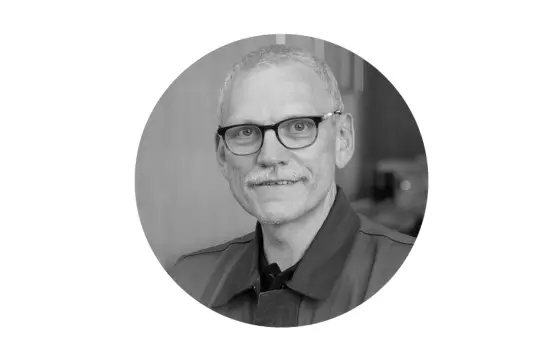
Günter Meyer is head of dynamic testing at our factory in Windsbach.
What is the minimum bending radius and what does this value tell me?
The minimum bending radius is the smallest possible radius to which the cable can be bent without damaging it. It is specified as a multiple of the cable diameter. The smaller the value, the more flexible the cable. There are several industry standards defining the minimum bending radii for different cable types. The values differ greatly, depending on whether the cable is used in a fixed or moving application. A drag chain cable of type MULTIFLEX 512-C-PUR UL/CSA, for example, has a minimum bending radius of 4 x d in a fixed application, but only 7.5 x d in moving one. The reason for this is that the bending stress in a permanently moving cable is significantly higher as the force and the direction of the bending motion are constantly changing. A suitable minimum bending radius is hence an important criterion when choosing cables and wires.
How can the flexibility of a cable be improved?
There are various ways to improve this, starting with using the best materials. In most cases, copper wires comprising of fine or finest stranded conductors are sufficiently flexible. Alloys can be used as well for some bespoke applications. Care must be taken that the insulation and sheathing materials are likewise flexible. The choice of materials makes a big difference, especially in applications at extreme temperatures. PUR or TPE sheathing are suitable for cold temperatures as they don’t get very stiff. The diameter and construction also have a major impact on the cable’s bending properties. The shorter the lay length, i.e., tighter twisting inside the core stranding, the more flexible the cable.